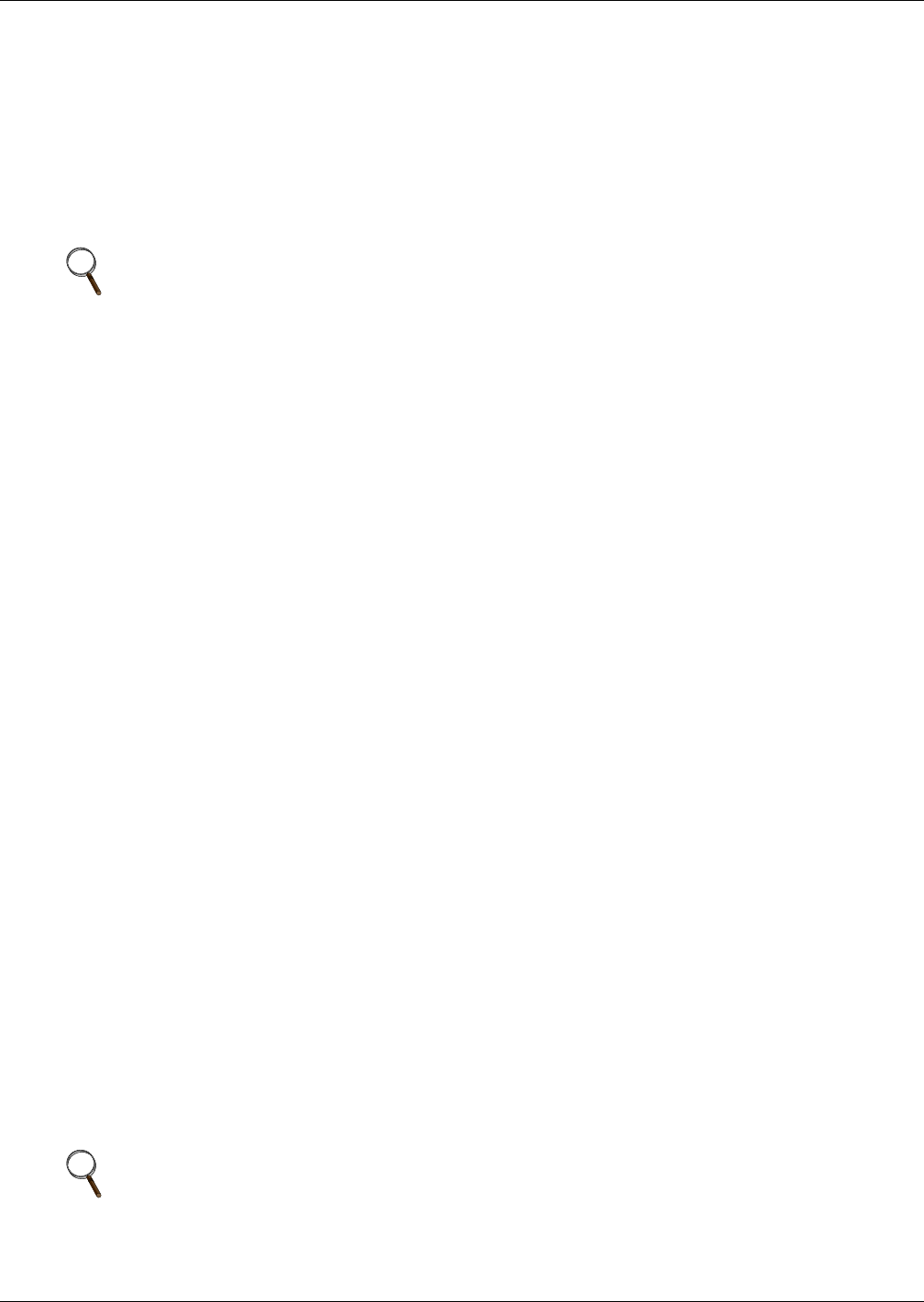
Operation
14
3.1.3 General Compressor Requirements
Low-Pressure Time Delay
When the compressor starts, the low-pressure input is ignored for a selected period of time based on
the setting of the Low Pressure Alarm Delay (Service Menu, Options Setup). This time is usually set
to 3 minutes on air-cooled units, and to 0 or 1 minute on water cooled units. When this time is
expired, a second timer starts to operate if the low-pressure input is active. This second timer is active
during normal compressor operation to avoid compressor trips due to bubbles in the refrigerant or
other influences creating short trips of the low-pressure switch. The low-pressure switch input is
enabled only if the compressor is operating. Exception: Pump Down (see Pump Down).
Pump Down
The Pump Down operation is performed to protect the compressor oil from being diluted with liquid
refrigerant to ensure that the compressor is properly lubricated for the next startup. The Pump Down
operation operates in the following manner:
Whenever a compressor is turned Off and the low-pressure switch is closed (pressure OK), the com-
pressor will be operated with the LLSV (liquid line solenoid valve) closed (de-energized) until the low-
pressure switch opens (low-pressure condition, without giving alarm). When there is a call to turn off
a compressor the LLSV is closed. If the low suction pressure switch (LPS) does not open within a spec-
ified time, the LLSV is turned On then back Off (to try to unstick the LLSV). The control will then
wait a set period of time for the LPS to open. This will happen three times. If, after three times, the
low suction pressure switch does not open, the compressor and LLSV are locked off and an alarm
“Pump Down not completed” will appear.
There is a re-pump down if the LPS opens again after the compressor has been already stopped—a
maximum of six re-pump-down cycles per hour are allowed. At the seventh request of re-pump down
the alarm “Comp 1 Pumpdown Fail” or “Comp 2 Pumpdown Fail” will appear and the compressor will
be locked out.
Pump down is always performed loaded (for compressors with unloaders: unloaders off, digital scroll:
control solenoid valve disabled).
For digital scroll only: when pump down has finished successfully (LPS opened), pump down will be
continued for another half-second with the control solenoid valve energized.
High Pressure Alarm
When the compressor is initially activated, the system will be monitored for a high pressure situation.
When a high pressure situation is detected during the first 10 minutes of operation, the unit will
attempt to correct the problem several times without notification. If the unit is unsuccessful in cor-
recting the problem, an alarm will occur and the affected compressor will be locked off. If high head
pressure alarm trips three times in a rolling 12 hour period, the affected compressor will be locked off.
After the compressor has been running for 10 minutes, if a high head pressure situation is detected,
an alarm will occur and the affected compressor will be immediately locked off without the unit trying
to correct the problem.
Once the compressor is locked off, it will not come back on until main power is reset, or until the
HP Alarm Counters (Service Menu, Diagnostics) are reset to 0. Setting the counter to 0 will auto-reset
the alarm without the need of pressing the reset button on the display. Even if the pressure in the
system drops below the alarm point, the compressor will remain off until the system is reset.
NOTE
Low-pressure condition could be read through contacts or through pressure transducers with
threshold setting.
NOTE
If the unit is equipped with manual reset high head pressure switches, or if the auto reset high
head pressure switches don’t reset, the compressor will not be turned back on, but there will be
a 30-second delay from when the high head pressure situation occurs and when the alarm is
annunciated.