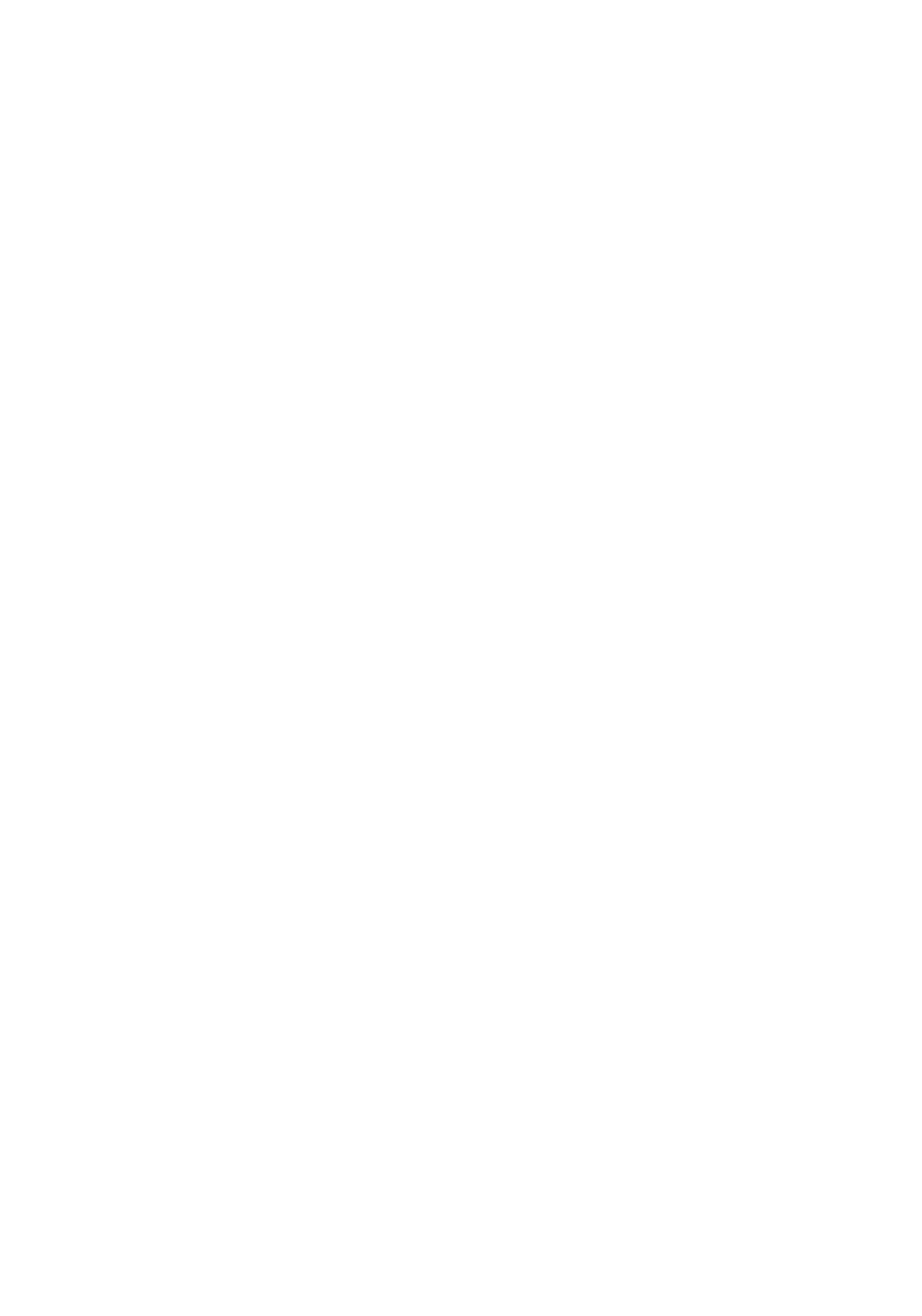
46
11.4 ORP SENSOR MAINTENANCE
11.4.1 Frequency of Cleaning
The frequency at which an ORP sensor should be inspected and cleaned can be determined only by experience.
If the process liquid coats or fouls the sensor, frequent cleaning may be necessary. If the process does not
contain a high level of suspended solids, the need for regular cleaning will be less.
11.4.2 Cleaning Procedures
The platinum electrode is easily cleaned by using a tissue to rub the metal surface with a paste of baking soda
(sodium bicarbonate). A clean platinum electrode is bright and shiny.
11.4.3 Checking the Reference Electrode
ORP electrodes manufactured by Rosemount Analytical have a silver/silver chloride reference. Section 12.3.3
describes how to check the performance of the reference electrode.
11.5 CALIBRATION
11.5.1 General
Many users regard calibration as a routine part of sensor/transmitter maintenance. Procedures for calibrating pH
sensors, ORP sensors, and general information regarding the use of pH calibration buffers and ORP standards
are given in Sections 10.0 Calibration of pH and ORP Measurements.
11.5.2 Calibration Frequency
The frequency at which sensors should be calibrated can be determined only by experience. Many factors influ-
ence calibration frequency. Sensors installed in dirty or corrosive process streams usually require more frequent
calibration than sensors used in clean water. Sensors measuring extreme pH values, particularly high pH, also
require more frequent calibration than sensors measuring mid-range pH. The width of the pH or ORP control
range and the consequences of an out-of-limits condition has a major influence on calibration frequency. The nar-
rower the control range and the greater the sensitivity of the process to control excursions, the more often the
sensor should be checked. Finally, if monitoring data are reported to regulatory agencies, the agency itself may
dictate the calibration frequency.
Use the following procedure to determine how often a pH sensor should be calibrated.
1. Calibrate the sensor. Record the date of calibration and the sensor response in buffers. That is, after calibrat-
ing, place the sensor back in the buffers and record the pH and temperature reading in each buffer. Also note
the value of the reference offset and slope.
2. Install the sensor in the process stream.
3. After the appropriate period—two weeks for a clean process, several days for a dirty or aggressive process—
remove the sensor and check its performance in buffers. Record the pH and temperature readings. The per-
formance of the sensor in buffer after it has been in service is called the as-found condition. Keeping a good
record of as-found data is an important step in determining the calibration frequency.
4. If the as-found data are acceptable, do not recalibrate the sensor. Return it to the process. Continue checking
the calibration at the same interval.
5. If the as-found data are not acceptable, recalibrate the sensor. After calibration, check the sensor response in
each buffer and record the results. Also note the reference offset and the slope. Return the sensor to service.
Check the sensor again after a period shorter than the one originally selected. For example, if the first interval
was two weeks, repeat the check after one week.
6. After a while it will become apparent how long the sensor holds calibration. The minimum calibration frequency
can then be determined.
7. Check the calibration of the sensor at least several times during the regular calibration interval. Interim
checks verify the sensor is still in calibration and validate the process measurements made since the last
calibration or calibration check.
MODEL 6081-P pH/ORP SECTION 11.0
MAINTENANCE