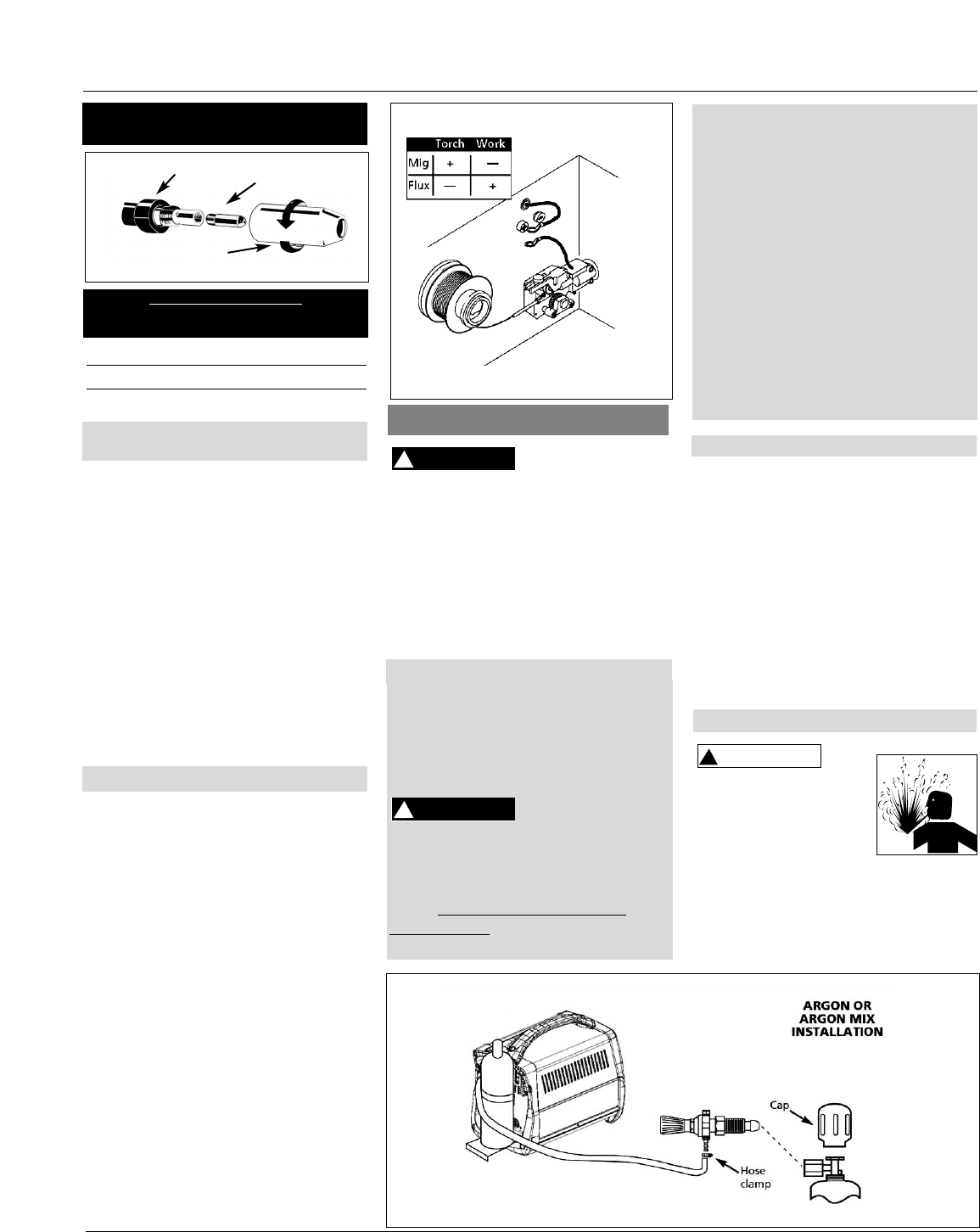
Improper handling
and maintenance of
compressed gas cylinders and regulators
can result in serious injury or death!
Always secure gas cylinders to tank
bracket kit, a wall or other fixed support
to prevent cylinder from falling over.
Read, understand and follow all
compressed gas and equipment
warnings in the safety instructions.
NOTE: Shielding gas is not required if
flux-cored welding wire is used.
There are 3 types of gas generally used
for gas metal arc welding; 100% argon,
a mixture of 75% argon and 25%
carbon dioxide (C25) or 100% carbon
dioxide.
Use ONLY the type
of gas
recommended for your welder. Use
ONLY an inert, non-flammable type of
gas. Failure to do so will result in a very
hazardous situation.
NOTE: 100% carbon dioxide is not
recommended due to unsatisfactory
weld beads.
!
DANGER
!
DANGER
The 75/25 mixture is recommended for
general steel welding. For aluminum
welding, use 100% argon. Cylinders of
either type gas may be obtained at your
local welding supply outlet. Secure
cylinder in place on your welding
machine or other support to prevent the
cylinder from falling over.
Obtaining Correct Gas Type. The gas
used in any welding application for your
welder must be an INERT, NON-
FLAMMABLE TYPE. You can get the type
of gas needed from a nearby welding
gas distributor (often found in the
yellow pages under “Welders” or
‘Welding Equipment”).
An adjustable regulator without gauges
is supplied with this welder. The
regulator provides a constant shielding
gas pressure and flow rate during the
welding process. Each regulator is
designed to be used with a specific gas
or mixture of gases. The argon and
argon mixture use the same thread type.
The 100% carbon dioxide uses a
different thread type. An adapter is
available at your local welding gas
supplier to change between the two.
Cylinder gas is under
high pressure. Point
cylinder outlet away
from yourself and any
bystanders before
opening.
1. With cylinder securely installed, stand
on side of cylinder opposite cylinder
outlet then remove cylinder cap and
open valve slightly by turning
!
WARNING
5
Welder duty cycle is the percentage of
actual weld time that can occur in a ten
minute interval. For example, at a 20%
duty cycle, actual welding can occur for
two minutes, then the welder must cool
for eight minutes.
Internal components of this welder are
protected from overheating with an
automatic thermal switch. A yellow
lamp is illuminated on the front
panel (on/off switch) if the duty cycle
is exceeded. Welding operations may
continue when the yellow lamp is no
longer illuminated.
To change between flux wire and MIG
wire the polarity must be changed.
1. Open the wire feed door.
2. Locate red (+) and black (-) polarity
connectors just above wire feed
mechanism (See Figure 7).
3. For MIG welding with gas,
connect torch cable from wire feed
mechanism to red (+) polarity
connector, then connect work cable
to black (-) connector.
4. For flux-core welding, connect
torch cable from wire feed
mechanism to black (-) polarity
connector, then connect work cable
to red (+) connector.
Contact Tip Markings
Mark Wire Size
0.6 mm .024"
0.8 mm .030”
0.9 mm .035”
Assembly (Continued)
Model WG2040, WG2044, WG2045, WG3000
DUTY CYCLE / THERMOSTATIC
PROTECTION
POLARITY
Shielding Gas Preparation
Figure 8 - Hookup
GAS TYPES
REGULATOR
HOOKUP PROCEDURE
Figure 7 - Cable connection
www.chpower.com
Torch Diffuser
Contact Tip
Nozzle
Figure 6 - Torch Nozzle